Parts of an Injection Moulding Machine
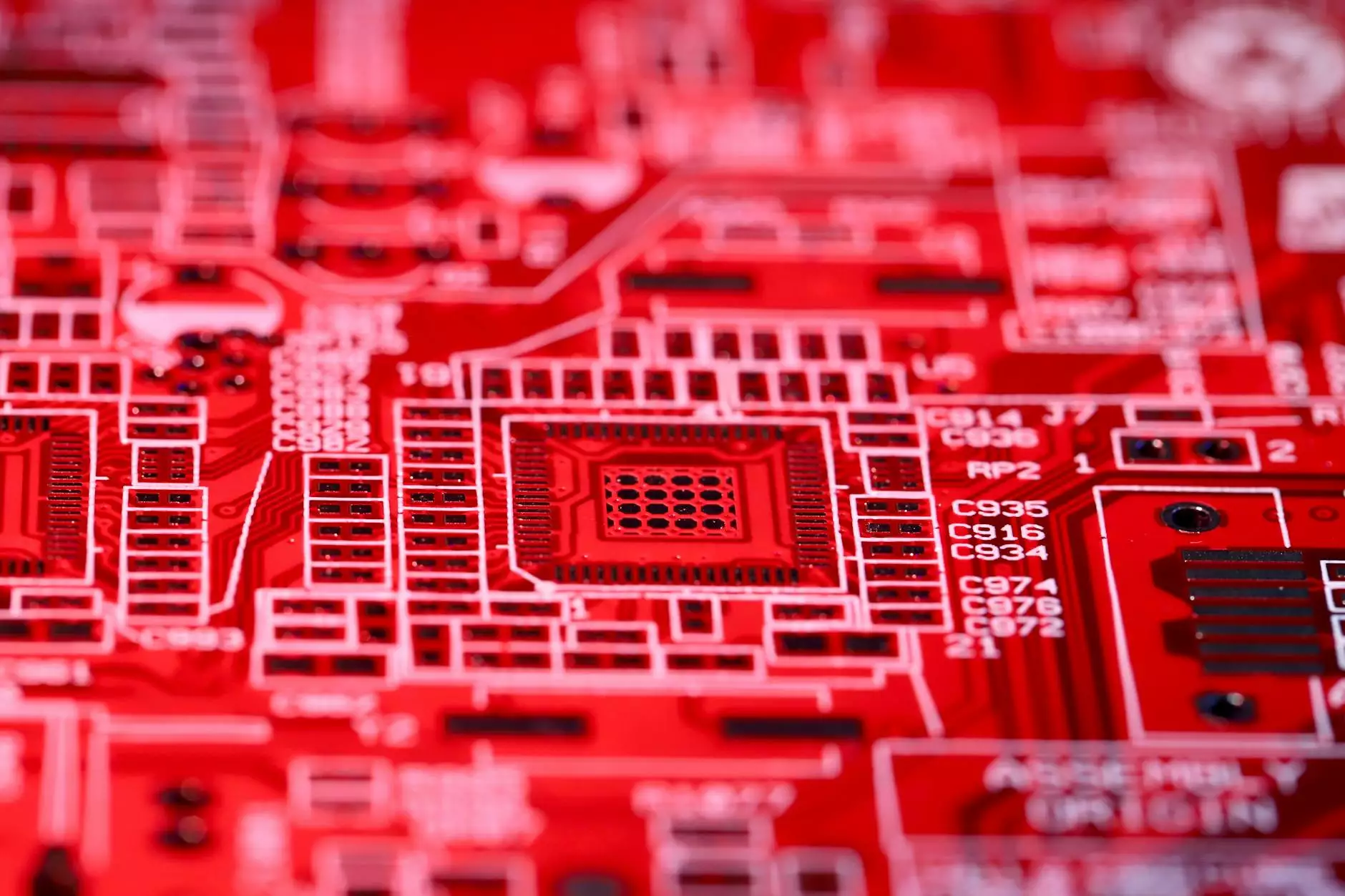
Welcome to Quick Parts, your premier destination for metal fabrication and 3D printing services. In this article, we will explore the various components that make up an injection moulding machine, one of the key tools in the manufacturing industry. By understanding the different parts and their functionalities, you will gain valuable insights into the intricacies of the injection moulding process.
Introduction to Injection Moulding
Injection moulding is a widely used manufacturing process that involves injecting molten material into a mould cavity to solidify and create a desired shape. This versatile technique is used to produce a range of products, from small intricate components to large industrial parts. An injection moulding machine, also known as an injection press, is crucial in executing this process.
Key Components of an Injection Moulding Machine
1. Hopper: The hopper is the initial reservoir where the raw material, typically in granular or powder form, is stored. This material is gravity-fed into the injection moulding machine, ensuring a steady supply of material for the production process.
2. Screw or Plunger: The screw or plunger acts as a means to transport the material from the hopper to the mould. In the case of a screw, it also serves the purpose of melting and homogenizing the material by applying heat and mechanical force.
3. Barrel: The barrel houses the screw or plunger and is responsible for providing the necessary temperature and pressure control during the melting and injection stages. It is often equipped with heating elements and cooling channels to achieve the ideal processing conditions.
4. Nozzle: The nozzle connects the barrel to the mould and allows the molten material to be injected into the mould cavity. It prevents leakage and ensures precise control over the material flow.
5. Mould: The mould, also known as the tool or die, is the cavity into which the molten material is injected. It is typically made of two halves, the core, and the cavity, which fit together to define the final shape of the product. The mould can be custom-designed to meet specific product requirements.
6. Clamping Unit: The clamping unit is responsible for securely holding the mould halves together during the injection and cooling processes. It applies the necessary force to keep the mould closed and withstand the pressure exerted by the molten material.
7. Hydraulic or Electric Power Pack: The power pack is the energy source that drives the various mechanisms of the injection moulding machine, such as the clamping and ejector systems. It applies the required force and provides the necessary control for smooth operation.
8. Ejector System: The ejector system helps remove the finished product from the mould once it has solidified. It consists of pins or rods that push the product out of the mould when it opens, allowing for easy retrieval and reducing downtime between cycles.
The Injection Moulding Process
Now that we have covered the key components, let's delve into the injection moulding process itself:
- Material Loading: The raw material is loaded into the hopper of the injection moulding machine, where it awaits processing.
- Melting and Injection: The material is heated and melted in the barrel, aided by the screw or plunger. Once molten, it is injected into the mould through the nozzle.
- Cooling and Solidification: After injection, the mould is subjected to a cooling process. This stage allows the molten material to solidify and take on the desired shape.
- Opening and Ejection: Once the material has solidified, the clamping unit opens the mould, and the ejector system pushes the finished product out.
- Repeat: The process repeats for the next cycle, as more material is loaded, melted, injected, cooled, and ejected.
Benefits of Injection Moulding
Injection moulding offers several advantages that contribute to its widespread use in the manufacturing industry:
- Versatility: With the ability to produce complex shapes and intricate designs, injection moulding is highly versatile and adaptable.
- Efficiency: The automated nature of injection moulding enables rapid production cycles, resulting in high output and cost-effectiveness.
- Precision: Injection moulding allows for tight tolerances and precise dimensions, ensuring consistent quality across batches.
- Material Variety: The process is compatible with a wide range of materials, including plastics, metals, and composites, offering flexibility in material selection.
- Sustainability: Injection moulding generates minimal waste as excess material can often be recycled or reused, making it an environmentally friendly manufacturing option.
Conclusion
Understanding the various parts of an injection moulding machine and their functions provides valuable insights into the injection moulding process. Quick Parts, your trusted source for metal fabrication and 3D printing services, utilizes the latest technologies and machinery to ensure precise and efficient manufacturing. With our expertise and commitment to quality, we deliver reliable solutions for all your production needs.
For more information about our metal fabrication and 3D printing services, visit quickparts.com.