Comprehensive Guide to Lathe Parts Description
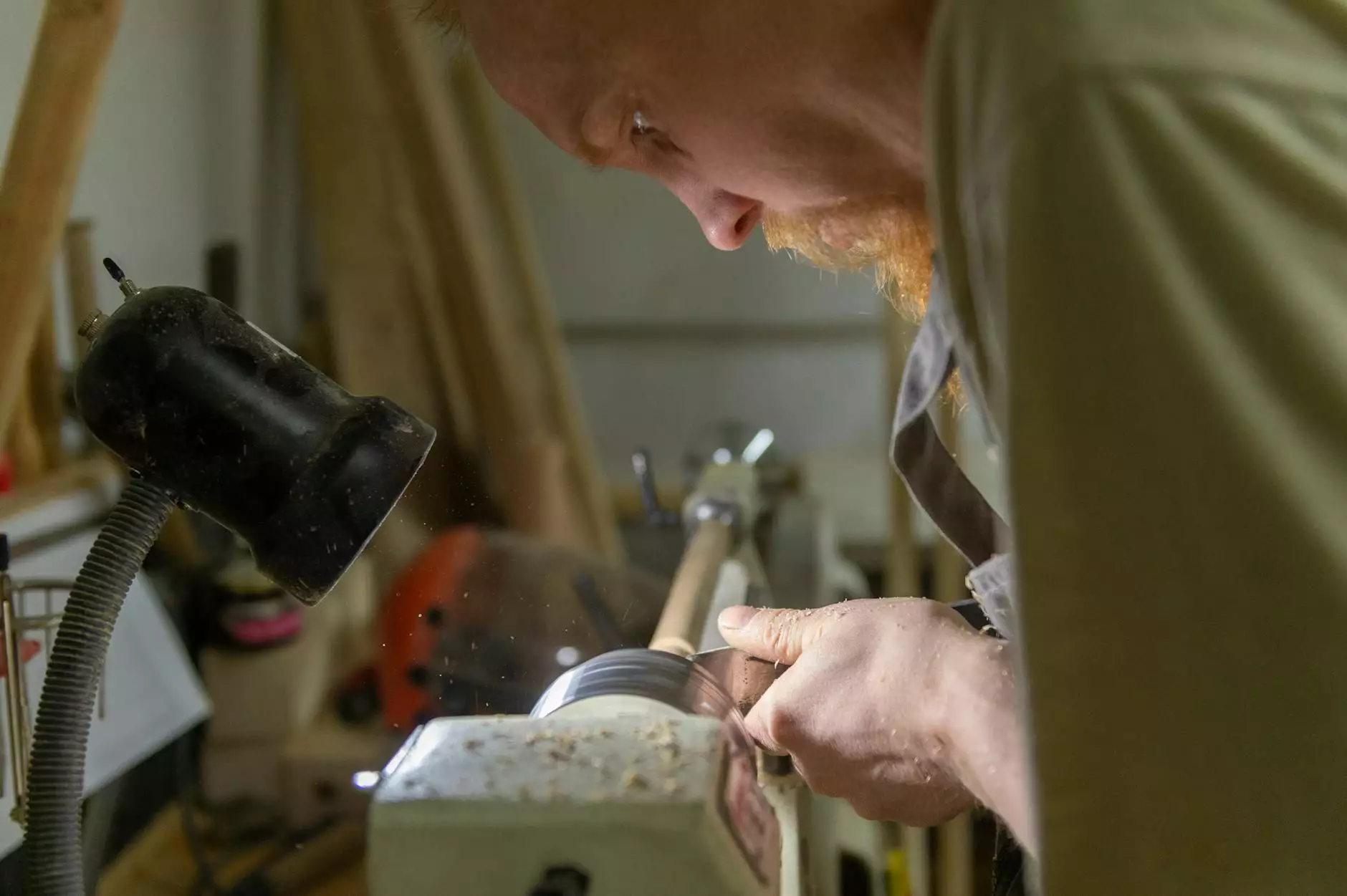
Understanding Lathe Parts
In the world of metal fabrication, a lathe is a crucial piece of machinery used for shaping and cutting materials, predominantly metals. The lathe operates by securing the material—typically a metal bar—spinning it around a stationary cutting tool, thus allowing for precise shaping and detailing of the material. To maximize the machine's efficiency and accuracy, understanding the individual lathe parts description is essential.
The Crucial Components of a Lathe
To gain a comprehensive understanding of lathe operations, let's delve into the various parts that comprise this remarkable machine. Below is a detailed description of key lathe components:
- Headstock: The headstock is the heart of the lathe, housing the main spindle that holds the workpiece. It often includes a gear mechanism that provides the lathe with variable speed control, allowing the operator to modify the rotational speed based on the task at hand.
- Tailstock: Located opposite the headstock, the tailstock supports the other end of the workpiece. This component can be slid along the bed to accommodate different lengths of material, and some tailstocks contain a center point or can hold tool attachments.
- Bed: The bed is the foundation of the lathe, providing stability and structural integrity to the machine. It is often made of cast iron or steel and is designed to minimize vibration during operation.
- Cross-slide: This is an adjustable platform that allows the cutting tool to move horizontally. The cross-slide is crucial for operations that require lateral cutting and shaping of materials.
- Compound Rest: A pivoting platform that allows for angular cuts, the compound rest can be adjusted to various angles. It is especially useful for turning and tapering operations.
- Carriage: The carriage houses the cross-slide and moves along the bed. It can be manually or automatically operated, depending on the lathe model.
- Chuck: The chuck is a clamping device attached to the spindle that holds the workpiece tightly in place. Chucks come in various types, including three-jaw chucks, which provide excellent centering ability, and four-jaw chucks, which allow for independent adjustment of each jaw.
- Tool Post: The tool post is a mount for the cutting tools. It allows for quick changes and precise positioning of tools for various machining operations.
- Spindle: This rotating part of the lathe holds the workpiece and is driven by the headstock. The spindle can support various speeds, making it versatile for different materials and operations.
- Feed Mechanism: This system controls the movement of the carriage and the cross-slide, allowing for automatic feeding of cutting tools across the workpiece, which increases efficiency.
The Important Role of Lathe Parts in Metal Fabrication
Every lathe part has a specific role that contributes to the overall functionality of the lathe. Understanding each lathe parts description is key to executing precise cuts and achieving high-quality results in metal fabrication. Here are a few examples:
Headstock Functions
The headstock is responsible for determining the speed and torque applied to the workpiece. Effective control over these factors is critical since different materials require different handling. The headstock's design must facilitate ease of operation while allowing for a firm grip on the workpiece.
Tailstock Versatility
Whether you need to drill holes at the end of a workpiece or support longer pieces during cutting, the tailstock is indispensable. Its adjustability allows operators to work with a wide variety of materials and sizes, boosting the lathe's flexibility.
Types of Lathes and Their Key Parts
Lathes come in different types, each tailored for specific applications. Understanding the configuration of lathe parts is crucial depending on the type of lathe being used.
- Engine Lathe: Often utilized in workshops, engine lathes are versatile machines with robust components. Their key parts, like the headstock and tailstock, are designed for high precision work.
- CNC Lathe: Computer Numerical Control (CNC) lathes integrate advanced technology for automated operations. They require more sophisticated parts and programming, allowing for complex designs and high output.
- Bench Lathe: Compact and often used for smaller projects, bench lathes have simplified parts that facilitate straightforward operations.
Advancements in Lathe Technology
Over the years, lathe technology has evolved significantly. Modern lathes now incorporate advanced materials, such as aerospace-grade alloys, and computer technology for automated operation.
Impact of Automation
With the rise of CNC technology, the efficiency and precision of lathe operations have drastically improved. CNC lathes often have enhanced lathe parts description that accommodate automated processes, reducing human error and increasing production rates.
Material Innovations
The composition of lathe parts themselves has seen improvements. The use of high-strength materials reduces wear and tear, prolonging the life of the lathe and improving output quality.
Common Lathe Parts Maintenance Tips
Maintaining lathe parts is essential for operational efficiency and longevity. Here are some essential maintenance tips:
- Regular Cleaning: Dust and debris can lead to wear and tear. Regular cleaning of the bed, carriage, and all moving parts is critical.
- Lubrication: Ensure all moving parts are adequately lubricated. This helps reduce friction and prolongs the life of the components.
- Alignment Checks: Regularly check the alignment of the headstock and tailstock to ensure accuracy in machining operations.
- Replacement of Worn Parts: Keep an eye on the spindle bearings and other wear components. Replacing them promptly reduces the risk of damage to other parts.
Conclusion: The Importance of Lathe Parts Description
In summary, a detailed understanding of the lathe parts description is vital for anyone involved in metal fabrication. Each part plays a unique role, contributing to the lathe's overall function and ability to produce high-quality finishes. By investing time in learning about these components and their maintenance, operators can ensure their lathes remain in top working condition, leading to exceptional outputs in their fabricating projects.
Whether you're a seasoned professional or just starting in metal fabrication, mastering the intricacies of lathe functionality is an invaluable skill that enhances your work and expands your capabilities in the field.