Investment Mold Casting Process: A Guide to Boost Your Business
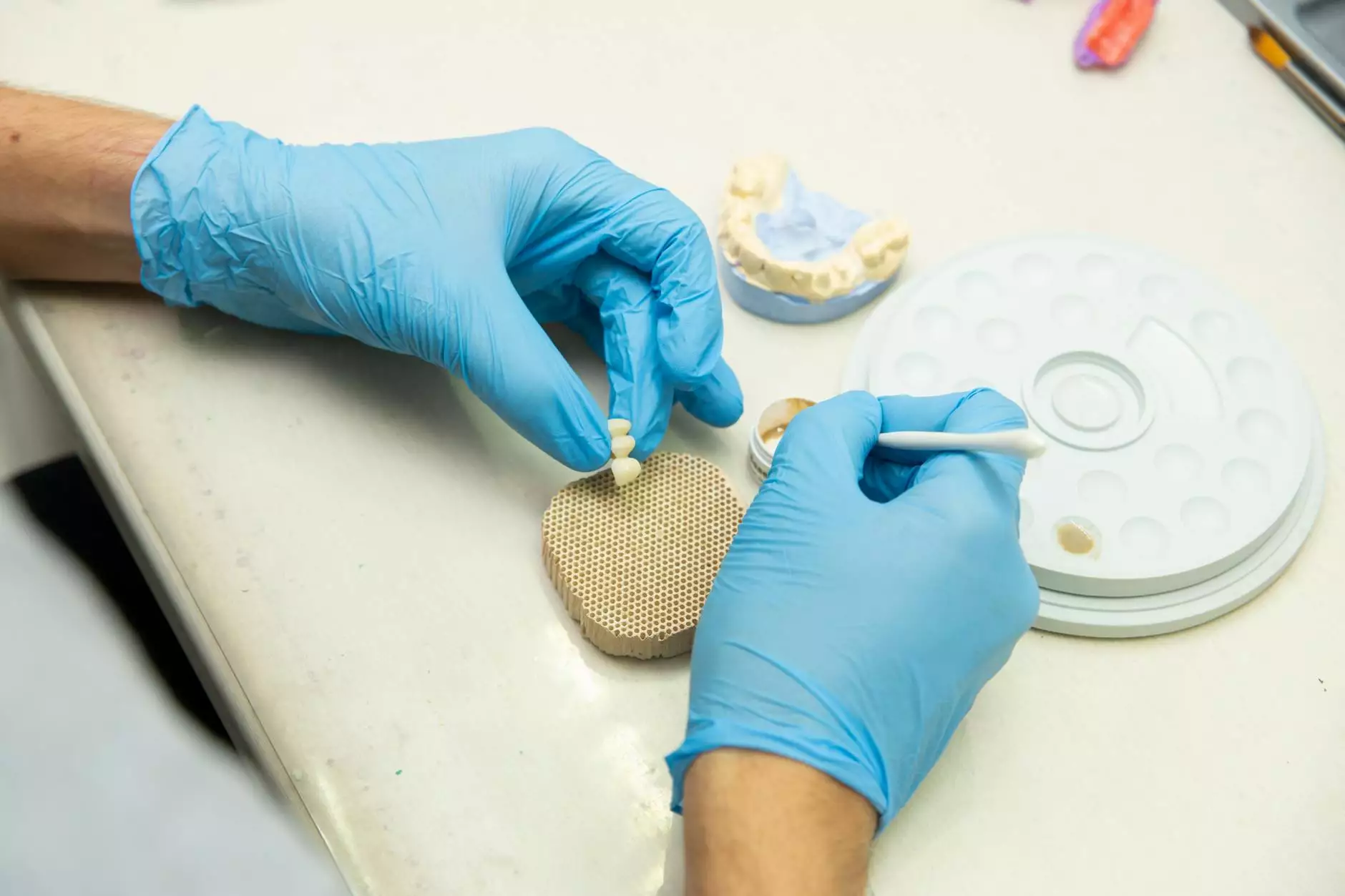
Introduction
Welcome to QuickParts.com, the leading destination for metal fabricators and 3D printing enthusiasts. In this article, we will delve into the fascinating realm of investment mold casting process, a technique revolutionizing the manufacturing industry. If you're looking to elevate your business to new heights, understanding and implementing this process can be a game-changer. So, buckle up and get ready to witness the power and versatility of investment mold casting!
What is Investment Mold Casting?
Investment mold casting, also known as precision casting or lost wax casting, is a highly precise and cost-effective manufacturing process used by metal fabricators. It involves the creation of a mold using a pattern or 3D printed model, which is then invested (encased) in a refractory material. The mold is then heated to remove the wax or pattern, leaving behind a cavity that is subsequently filled with molten metal. Once the metal solidifies, the mold is broken, revealing the final cast product.
This process offers exceptional accuracy, intricate detail reproduction, and excellent surface finish, making it a preferred choice in industries such as aerospace, automotive, medical, and more. Let's dig deeper into the various stages and benefits of the investment mold casting process.
The Investment Mold Casting Process Explained
The investment mold casting process involves several stages, each crucial for obtaining high-quality castings that meet specific requirements:
- Pattern Creation: In this initial stage, a pattern is created to replicate the desired product. The pattern can be made using various materials, including wax, plastic, or resin. 3D printing technologies have revolutionized this stage, allowing for intricate and complex patterns with incredible precision.
- Mold Assembly: The pattern is embedded in a casting flask, which is then filled with a fine and moisture-resistant molding material. This material, usually made of ceramic, silica, or plaster, solidifies around the pattern, forming the investment mold.
- Wax Removal: Once the mold has fully set, it is heated to remove the wax pattern, leaving behind an empty cavity ready for metal casting.
- Metal Pouring: The investment mold is preheated to a specific temperature to ensure optimal metal flow and minimize defects. Molten metal, such as steel or aluminum, is poured into the mold via sprues, gates, risers, and runners.
- Cooling and Solidification: The metal fills the cavity, solidifies, and cools down. The solidification process may be controlled to achieve desired mechanical properties and minimize internal stresses.
- Mold Breakout and Finishing: Once the metal has cooled completely, the investment mold is broken, revealing the newly cast part. Depending on the complexity and intricacy of the part, finishing processes such as grinding, polishing, or machining may be applied.
Advantages of Investment Mold Casting
The investment mold casting process offers numerous benefits, making it a highly sought-after technique in various industries:
1. Exceptional Dimensional Accuracy
Investment mold casting allows for incredibly precise replication of intricate details, achieving high dimensional accuracy that is often challenging to achieve with other casting methods. This precision is crucial for industries such as aerospace and medical, where even the tiniest deviations can have significant consequences.
2. Versatile Material Selection
One of the significant advantages of investment mold casting is the extensive range of materials that can be used. From stainless steels to aluminum alloys, titanium, cobalt-chromium, and more, this process accommodates multiple materials, providing flexibility to meet diverse application requirements.
3. Excellent Surface Finish
The investment mold casting process produces parts with exceptional surface finish and minimal post-processing requirements. This feature not only saves time and resources but also ensures superior aesthetics and functionality of the final product.
4. Complexity without Compromise
Thanks to advancements in pattern creation techniques, investment mold casting allows for the production of complex and intricate parts with ease. The process can capture even the most intricate geometries, enabling designers and engineers to bring their innovative ideas to life without compromising on structural integrity.
5. Cost-Effectiveness
Investment mold casting offers an excellent cost-to-benefit ratio. The use of reusable molds, reduced material wastage, and minimized post-processing requirements contribute to overall cost savings. Additionally, the ability to produce multiple parts simultaneously further enhances productivity and cost-efficiency.
Applications of Investment Mold Casting
The investment mold casting process finds applications across various industries, where precision and high-quality castings are prerequisites:
Aerospace
From critical engine components to complex turbine blades, investment mold casting plays a vital role in the aerospace industry. Its unmatched dimensional accuracy, superior mechanical properties, and ability to produce lightweight parts make it ideal for aerospace applications.
Automotive
Investment mold casting is utilized in the automotive industry for manufacturing engine components, suspension parts, transmission housings, and more. By facilitating the production of intricate shapes and reducing weight while maintaining strength, investment mold casting contributes to increased fuel efficiency and superior performance.
Medical
Precision is paramount in the medical field, and investment mold casting delivers exceptional results when it comes to medical device manufacturing. The process is widely used for producing implants, prosthetics, surgical instruments, and other critical components that demand high accuracy and biocompatibility.
Industrial and Engineering
Investment mold casting finds applications in various industrial and engineering sectors, including oil and gas, power generation, and equipment manufacturing. From highly wear-resistant pump components to heat exchanger parts, investment mold casting fulfills the stringent demands of these industries.
Conclusion
The investment mold casting process has emerged as a game-changer, revolutionizing the manufacturing industry. Its exceptional dimensional accuracy, versatile material selection, outstanding surface finish, and cost-effectiveness make it a highly sought-after technique for metal fabricators and 3D printing enthusiasts alike. By embracing this groundbreaking process, businesses can unlock new possibilities, enhance product quality, and gain a competitive advantage in today's rapidly evolving market.
At QuickParts.com, we specialize in providing top-notch investment mold casting services, along with a wide range of metal fabrication and 3D printing solutions. Contact us today to explore how our expertise and cutting-edge technology can help you achieve your manufacturing goals!